Embracing change: Breaking down the process of flexible manufacturing
Udgivet kl. 30. januar 2024 i Flexible Manufacturing
The fast-moving consumer goods market is experiencing a transformative shift, driven by factors such as consumer empowerment, customization demands, health-conscious preferences, veganism, ethical concerns, and sustainability. We expect that it will undergo more changes in the next decade than it has in the previous 50 years. This necessitates the adaptation of production and supply chains to meet emerging trends. The future of fast-moving consumer goods factories will likely involve smaller, smarter facilities with autonomous movement of goods and interconnected systems.
Machines, whether standalone or interconnected, need to be more flexible than ever before to ensure the timely supply of appropriate materials and packaging. Production has to be more agile, increasingly producing retail-ready items with a high mix-low volume approach with zero recalls. The question is how to realize this with minimal cost and fast ROI?
Workflow in three levels
To achieve the optimal solution with maximum flexibility, it is important to consider various factors. A practical approach, like the one employed by OMRON, focuses on optimizing processes to minimize disruptions. This involves breaking down the workflow into three functional levels.
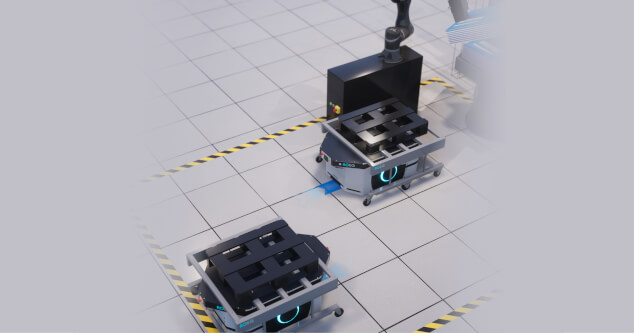
Level 1 - For the machine - Intralogistics
Before reaching the production line and machine level, the emphasis needs to be on enabling flexibility in the production line, thanks to just-in-time delivery of consumables, optimizing the transport of goods, boxes, and pallets, as well as managing half-products, waste, and unused consumables. The goal is to avoid storing consumables and half-products on the shop floor.
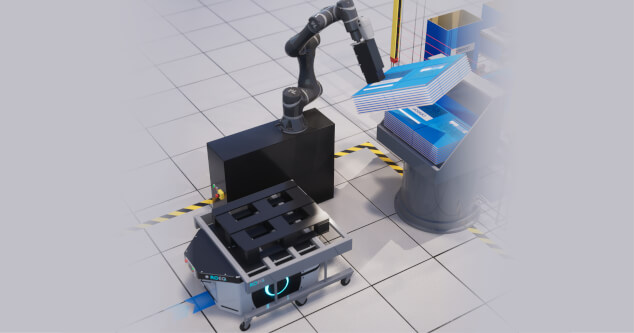
Level 2 - At the machine - Machine feeding
At the machine level, the focus shifts to automating material verification and feeding processes, replacing manual feeding activities with automated ones, conducting quality assurance on packaging materials, and ensuring package integrity after packaging.
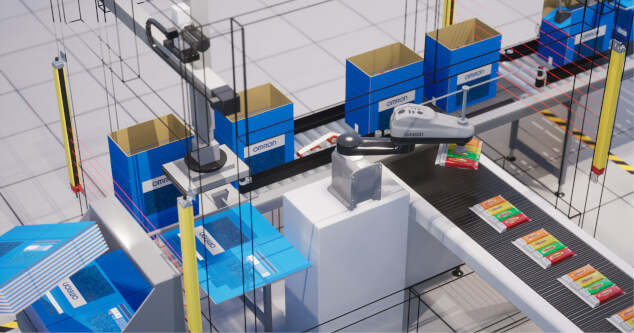
Level 3 - In the machine - Machine setup
In the machine itself, all functions such as machine control, motion, robotics, sensing, vision, and safety are automatically aligned. This ensures that tasks like filling, capping, tray loading, seaming, sealing, and labelling are executed as quickly as possible, thereby enhancing overall efficiency.
The Benefits
The automation of production processes for flexible manufacturing offers numerous advantages, including:
- Faster product change-over capabilities enable quick adjustments and modifications to production lines, reducing changeover time and optimizing performance
- Improved tracking and analysis provide valuable insights for continuous improvement and workflow optimization.
- Increased employee satisfaction thanks to focus on value-adding tasks and more strategic and creative work